MSU-1 GC is constantly identifying and implementing cutting-edge construction technologies, a strategy that drives its growth as a competitive and innovative company in the rapidly changing construction industry. The Company has an effective vertically integrated business model and leverages all the benefits of combining the roles of the general construction contractor, EPCM contractor, and manufacturer of certain types of building materials.
MSU-1 GC and its partner organisations have their own production facilities manufacturing translucent structures and unitised curtain walls and plan to produce doors at different price points at SEZ Zelenograd. In addition, through synergies with FSK Group, the Company can use materials produced by the group’s enterprises at construction sites, spanning glass, concrete, mortars, cement and sand mixtures, reinforced concrete wall slabs, and curtain walls.
In the coming years, the Company intends to launch additional production facilities manufacturing façades and all types of doors to meet more than 70% of the demand for these building materials from its current projects. This will reduce construction timeframes and costs of MSU-1 GC projects while also boosting value for money.
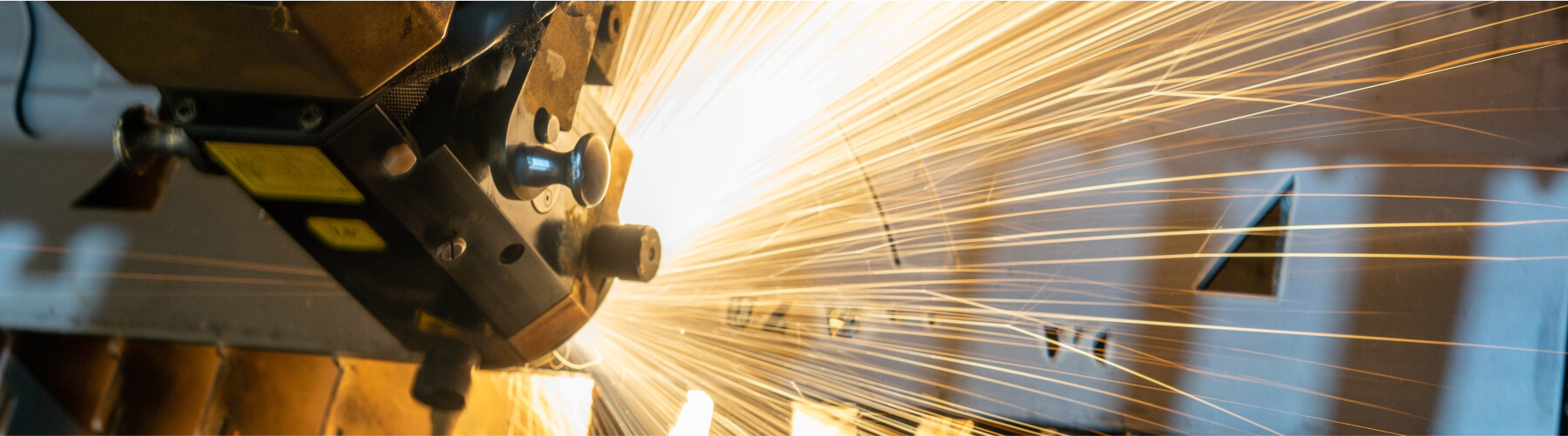
Synergy with FSK Group
MSU-1 GC is part of FSK Group, which has its own production of glass, concrete, reinforced concrete wall slabs, and curtain walls.
Glass production
At various construction projects, MSU-1 GC uses glass produced by Guardian Glass.
Guardian Glass has two enterprises, acquired by FSK Group in 2022 and located in Ryazan and in the Rostov Region. As some of the most advanced float glass facilities in the industry, they are capable of producing 1,650 tonnes of glass per day.
Their product mix includes multifunctional, transparent polished, energy-efficient, and solar control glass. Advanced methods and technologies are used to produce glass at these facilities, allowing the most original designer concepts to become a reality.
Concrete production
About 50%–60% of the concrete mixtures used by MSU-1 GC in construction are supplied by AO TD Partner.
The company is part of FSK Group and one of the leading suppliers of concrete mixtures in the Moscow region. AO TD Partner produces high-quality ready-mixed concrete, mortars, cement and sand mixtures, and reinforced concrete products. AO TD Partner has a four-stage production quality control system: concrete mixtures are checked by the chief process engineer, then by specialists of the company’s own laboratory, with testing conducted on specialised scales, and assessments carried out by foremen when unloading products at the construction site.
Production of reinforced concrete structures, wall slabs, and curtain walls
MSU-1 GC actively deploys prefabricated solutions developed by AO DSK-1, part of FSK Group. Such solutions are used not only in prefabricated buildings but also in in-situ concrete construction, for example as curtain walls or individual elements of the building structure.
DSK-1 has three enterprises that produce various types of reinforced concrete products: Rostokinsky Plant of Reinforced Concrete Structures, Novokhokhlovsky Plant of Reinforced Concrete Products, and Voskresensky House Building Plant. All plants have undergone a large-scale upgrade programme in line with global best practices of industrial production.
Own production capacities
MSU-1 GC and its partner organisations have advanced facilities producing unitised curtain walls, translucent structures, and doors.
Production of unitised façades
MSU-1 GC works with advanced façade solutions. In particular, the Company cooperates closely with the Genesis production complex located in Yasnogorsk, Tula Region, and focused on unitised façade solutions and materials.
The Genesis unitised curtain wall system is a complete self-supporting element of a building. Its design is based on the technology used in manufacturing G-Tech large-format unitised curtain walls, fully assembled and ready to be installed following the “building set principle”. Such façade systems and structures help maximise construction rates, fundamentally improve the quality of installation, and implement the boldest projects and design solutions. Among other things, the technology drives a 10x increase in labour productivity when constructing façades and cuts installation times by 50%–70%.
Production of translucent structures
The Company has its own production facility manufacturing translucent structures made from aluminium profile, with a capacity of about 15,000 m2 per month. The Company uses high-tech Italian equipment to manufacture window and door units, entrance and glazing solutions, pitched structures for roofs, winter gardens, and skylights, as well as unitised façades.
Door manufacturing
The Company plans to further develop its technology capacities. Construction of its own technology park at SEZ Zelenograd will be launched in 2023 to meet the Company’s internal needs. In particular, the technology park will produce a wide range of doors at different price points, from economy to premium. High quality – coupled with cost and overhead optimisation – will support one of the most attractive competitive offers in the industry.